Crisis Management at IQUW
The rapid proliferation of electric vehicles (EVs) and the increasing integration of advanced electronics in car manufacturing have significantly transformed the automotive industry. However, these advancements bring forth a new set of challenges, particularly in the realm of product recalls.
As vehicles become more complex, the potential for electronic and software-related malfunctions rises, necessitating a more sophisticated and efficient approach to identifying, managing, and executing recalls. This evolution not only tests the current recall infrastructure but also demands an enhanced focus on ensuring safety, reliability, and regulatory compliance amidst a swiftly changing technological landscape.
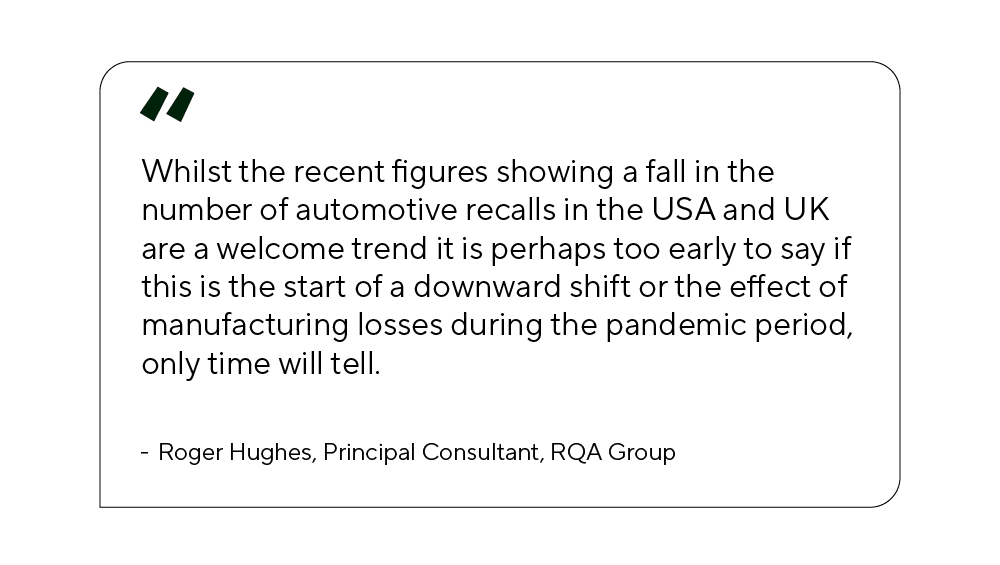
From combustion to computer
While crude electric carriages were first invented in the late 1820’s it hasn’t been until the early 21st century that interest and demand for electric cars has substantially grown.
Technology found within both internal combustion engine (ICE) and electric vehicles (EVs) has developed at a rapid pace. With this speed of change and constant upgrading of parts and software it becomes important to understand the intricacies of product recall risk associated within the automotive sector.
According to National Highway Traffic Safety Association (NHTSA), the number of safety product recalls was down for 2023 versus 2022 – however, the total number of vehicles recalled was up. So, while frequency is down, the severity is up where we have entire vehicles being recalled. “Once again though recalls are trending up for 2024 suggesting this could be the highest number of recalls for at least 12 years.” Read the RQA report here.
The shift towards electronification in automobiles has been a gradual yet transformative process. Today, approximately 80% of a light vehicle comprises electronic components, signifying a shift in automotive design and functionality.
While the transition to EVs is predominantly driven by environmental concerns and government mandates, it also presents a host of novel challenges, particularly in terms of engineering knowledge, product safety and quality assurance.
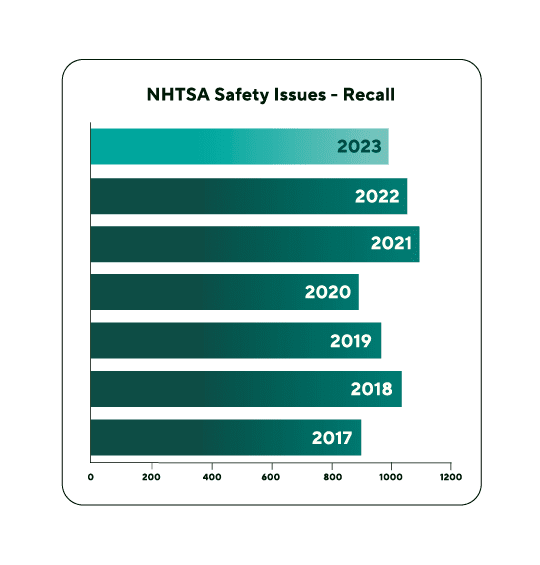
Component at fault
One of the primary challenges stems from the intricate nature of EV componentry, notably lithium-ion batteries. These high- energy-density power sources, while revolutionary in their capabilities, also pose inherent risks. With intense competition driving manufacturers to produce lighter, more efficient batteries at a lower cost, the pressure to innovate often outpaces the ability to thoroughly test and validate new technologies. The result is a heightened risk of safety incidents, including overheating and potential thermal runway—a reality underscored by recent recalls in the industry affecting vehicle populations in the hundred thousands.
With batteries costing up to $10,000, this creates a significant increase to the cost of product recalls to repair or replace the batteries, resulting in claims well into the millions of dollars.

Whilst ‘Electrical system’ is a broad category, they remain responsible for the most recalls by some margin
Disruption
Compounding the challenge of rapid product development is the increasingly complex global supply chain, which has been further strained by a variety of factors:
Pandemic: National lockdowns globally caused by the outbreak of Covid-19 meant the supply of raw materials and finished goods were slowed or temporarily stopped between 2020 and 2022. We could see a repeat of this if there were to be another pandemic.
Cargo: Suez Canal both blockage and the current Red Sea shipping crisis has continued to cause major disruption in the movement of goods with 30% of global container trade transiting through the area.
Global political events: Russia-Ukraine war triggering sanctions along with hampering trade route operations and critical logistics. There are also ongoing territorial tensions in Taiwan could further impact key supply chains.
Catastrophes: In 2024 significant catastrophic events have impacted critical infrastructure relevant to the automotive industry. The collapse of the Baltimore bridge, a vital conduit for one of the United States’ largest ports, has had considerable repercussions for the US auto market. Additionally, the earthquake in Taiwan, a key global hub for semiconductor manufacturing, led to a temporary halt in production, further straining the supply chain.
From sourcing raw materials to manufacturing critical components, automotive supply chains are constantly susceptible to a myriad of disruptions that can ripple through the entire production process. These disruptions not only lead to delays in vehicle production but also force original equipment manufacturers (OEMs) to seek alternative suppliers risk.
that uses sensors and cameras to aid road safety, i.e. adaptive cruise control, and other critical vehicle functions, has exposed vulnerabilities in the automotive industry’s supply chain resilience.
The reliance on fabless (where manufacturing is outsourced to a third party) semiconductor manufacturers, coupled with geopolitical tensions and export restrictions, has further exacerbated the semiconductor shortage, creating a ripple effect felt across the entire automotive ecosystem.
Mitigation
In light of these challenges, stakeholders across the industry must adopt a proactive approach to mitigate product recall risk. Core question need to be asked:
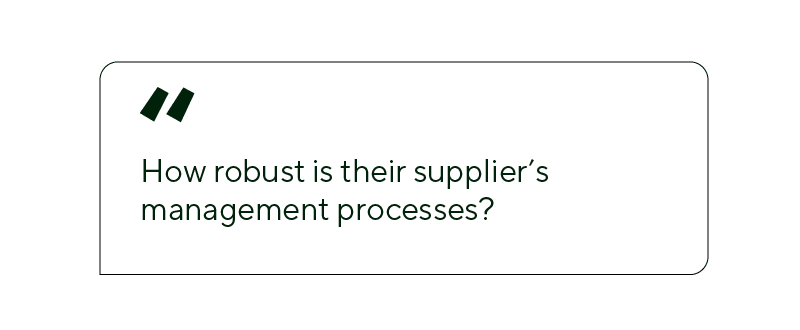
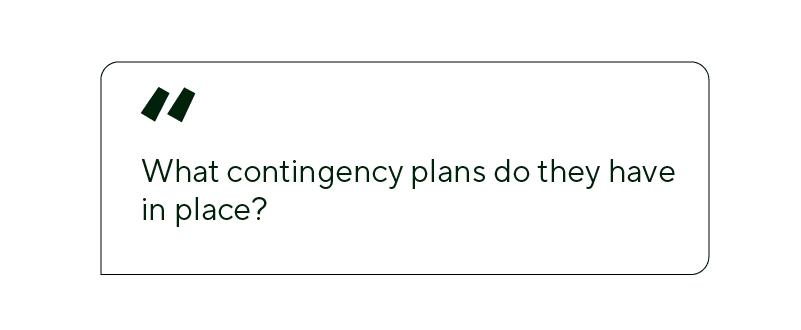
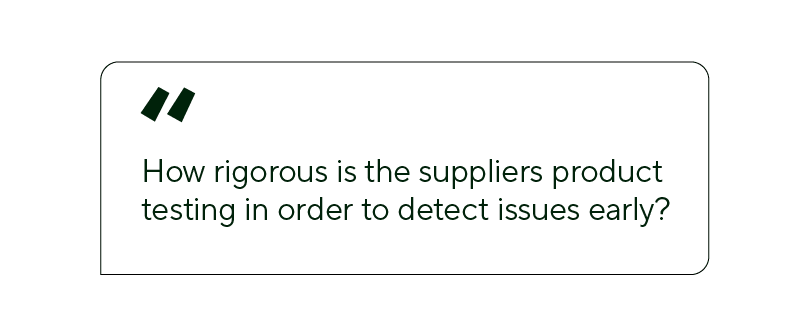
This is due to forecasting models being “statistical-dynamical” in nature – meaning that despite having a backbone of a proper numerical weather model, some weight is given to statistics and parametrizations (i.e. internal model approximations). It’s done because numerical model is not sufficient to forecast RI on its own and needs to rely on this additional information.
Furthermore, the emergence of software- driven technologies presents a new frontier in automotive risk management. As vehicles become increasingly reliant on complex software systems, the importance of skilled technicians cannot be overstated.
Addressing the skills gap in software engineering and investing in comprehensive testing infrastructure are critical steps in mitigating the risks associated with software-related recalls.
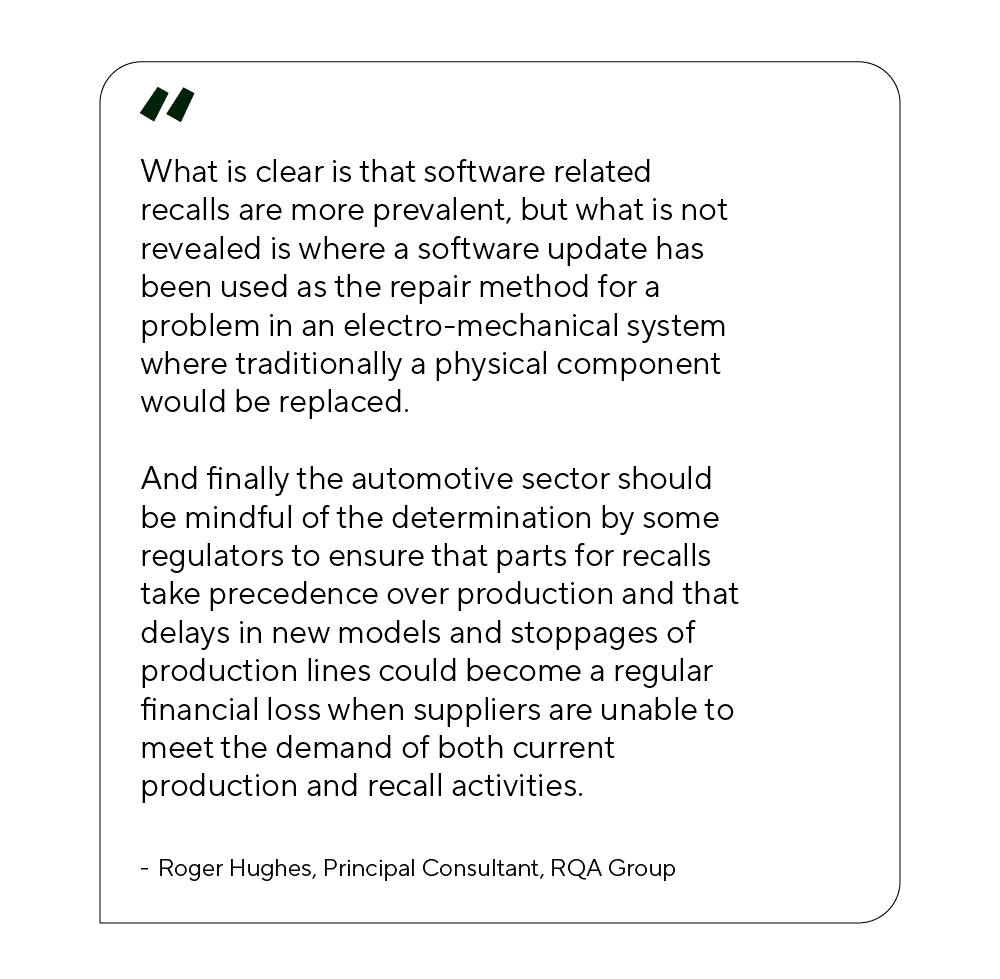
ADAS pressure points
Another area of concern is ADAS design issues. ADAS technologies, including safety features such as adaptive cruise control, lane-keeping assistance, and automatic emergency braking, are heralded as the future of automotive safety, promising to reduce accidents and improve road safety. However, the integration of these systems has created a new dimension of risk for insurers.
Design flaws or malfunctions in ADAS components can have far-reaching consequences, potentially leading to systemic issues across a fleet of vehicles. Design-related recalls have greater potential to affect a large population of vehicles simultaneously. This systemic risk poses significant challenges for insurers, as widespread recalls can lead to substantial financial liabilities and reputational damage.
Tesla in 2023 recalled more than two million cars after the US regulator found that its driver assistance system, Autopilot, was partly defective. Whilst a software update should be an easy and quick fix (conducted remotely with an over-the-air update, versus physically recalling the vehicles which can extend to years), the numbers are scary – one of the largest ever recalls in the US.
To effectively manage the risks associated with ADAS and design issues, insurers must prioritise proactive risk assessment and mitigation strategies. This includes conducting thorough evaluations of ADAS components during underwriting processes, as well as ongoing monitoring of emerging safety concerns and regulatory developments.
Collaboration with automotive manufacturers and industry experts is essential to stay abreast of technological advancements and ensure that insurance policies are appropriately aligned with evolving risk profiles. As we’ve seen with Tesla, software within electrical components is ever important and manufacturers need to upskill in these areas to keep up to speed.
Crisis Management
June 2022 marked the debut of IQUW’s crisis management insurance programme, crafted to help businesses predict, mitigate, respond to, and recover from numerous risks. This class of business is managed by Jon Atkinson, an expert specialty underwriter with extensive experience.
Partnering with the renowned RQA Group, experts in product risk and crisis management, IQUW enhances its Specialty Product
Recall coverage with RQA’s global consultancy. RQA Group offers 24/7 incident support and pre-incident risk management services to IQUW policyholders, alongside providing risk engineering and claims support to IQUW’s crisis management team.
Crisis Management insurance is particularly relevant in the context of the rapidly evolving automotive sector, where the intricacies of product recall risks are critical.
While every crisis is different, most demand immediate action. That’s why our comprehensive cover ensures a swift response every time. IQUW can provide product recall insurance solutions for a variety of manufacturing sectors, including the automotive industry.
For more information
Download our Crisis Management Appetite Sheet or contact one of our underwriters.
Jon Atkinson
Lead Underwriter Crisis Management
jon.atkinson@iquw.com
